There are so many autobody repair businesses raising the bar for the industry, standards climb each year. Deciding on the national winners is no easy task.
How do we choose who wins in their category? The national best shop winners in each category are drawn from the state winners. To be a state winner you already have to excel in every aspect of the judging criteria, so what tips a business over the edge to superstardom?
It’s a combination of factors including having a clear vision for the business, attitudes towards staff, innovative ways of doing business and a positive go-getter attitude. We say it every year, these awards are not a beauty contest – although there might be an element of that for the new shop category. We visit shops during working hours and, now the judging team has nearly 20 years experience between them, notice if staff are happy and productive. If the workshop is reasonably clean and well organised, with equipment and consumables easy to find and in good order that goes a long way towards the happy productive staff.
Dirty shops can’t be as efficient as cleaner businesses especially as dirt is the enemy of the spray painter and a waster of valuable time and therefore profit if endless denibbing is needed to get the vehicle up to scratch. A clean orderly workshop also indicates a healthy staff culture - team members who take pride in and have respect for their workplace.
Our national winners tend to be involved in their community and in the industry. They take their blinkers off and try to foster as many beneficial relationships with suppliers, work providers and other repairers. They take time to attend events which could inspire them or increase their knowledge.
This year’s winners all have different personalities and different business models. What they do have in common is total focus, a steel will to succeed, an obsessive need to constantly improve processes and facilities, dedication to quality and customer satisfaction and a Trojan work ethic.
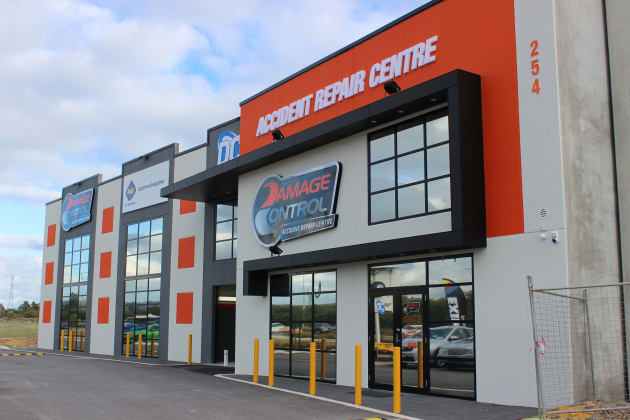
BEST NEW SHOP Damage Control
Alright, the fact that Damage Control Accident Repair Centre in Forrestdale WA is ridiculously gorgeous (a word not often associated with autobody repair facilities) didn’t go against it. Stunning exterior in bold, eye-catching orange livery, plenty of parking, contemporary, attractive business logo are all ticks. But build this business frontage so that it faces 33,000 potential customers who drive by daily and you’re definitely onto something.
It’s a bold step to move the business to another suburb and start from scratch – but they do say that fortune favours the brave. A definite industry trend is reception areas that would put boutique hotels to shame. Eagle Smash Repairs in Queensland and the majority of our winners would make many a customer walk outside to check they were in the right place. Damage Control doesn’t disappoint here, or in the boardroom upstairs or in the offices. However it is the workshop where the team’s passion for the business shines brightest. State of the art everything here, beautifully laid out for optimum workflow. Anthony Arnold has built his dream shop, hell he’s built a lot of people’s dream shop and it was undoubtedly a big investment. However, nothing is over the top, just beautifully designed and executed. The mechanical and tyre offering is a great way to build relationships with customers so the business is front of mind if they do have an accident. What Arnold has achieved here is making his business stand out in a relatively small WA crowd and we imagine that this will help his investment pay off.
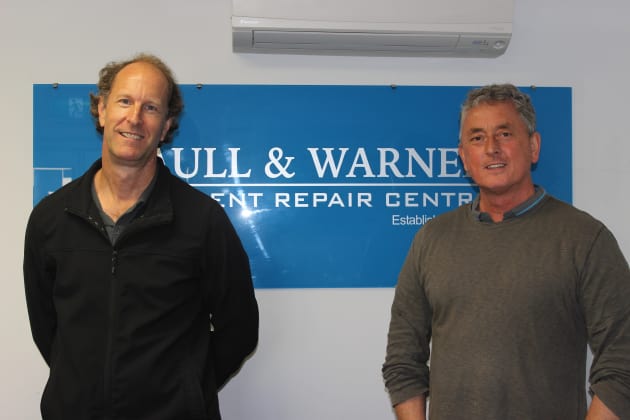
Best boutique shpP Axalta Sustainability award Paull & Warner
WA did well this year in the nationals with Paull & Warner in Belmont snabbing Best Boutique. It was very close as Bennett Elder in Sydney also really impressed the judges.
Business partners Nick Farago and Heath Barber have seen the wind blowing towards MSOs and decided to step into the breeze. Their second shop is stylish, practical and well kitted out with a keen emphasis on customer comfort. Both benefit from careers in the supplier chain which allowed them to visit a huge range of repair shops and observe what works and what doesn’t. That the pair impressed us with their sustainable business practices is evident in it collecting the Axalta Sustainability award this year – we will cover this in the January issue. A lot of thought, planning as well as heart and soul have been invested in the business – we’ll be keeping an eye out for shop number three in the next couple of years.
Best Medium Shop Best Customer Experience Len Hollis Repair Facility
Darren Myers has created an exceptional customer-focussed business, so much so that he also won the best customer experience award. Another way that our national winners stand out is that they often don’t follow industry trends but set them. Myers has had an ipad bar for a couple of years now. We loved the open dealership-style reception desk instead of a counter. The whole of reception is soothing which is what you want if you’ve had an accident. There’s a baby changing table in the outrageously opulent toilets and even a difiribulator in the hallway. Mortlake is a wealthy suburb and Myers has pitched it just right. Staying a step ahead is a mindset – has he repaired any electric cars yet? No. But he’s installed a car charger so he’s ready when the opportunity arises. He was another early adopter of the curtained aluminium repair bay. Forward thinking and customer-focussed – if you’re a manufacturer or a work provider what’s not to love?
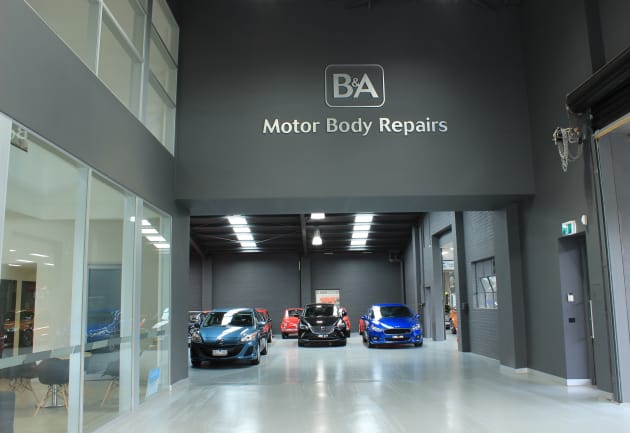
Best Large Shop B&A Motor Body Repair
This is a huge site in Melbourne which has grown organically over decades. This family business radiates a passion for cars, quality and customer service. Offering full mechanical services enlarges the customer base. The Mazzeos’ (pictured below with James Frape from Compass Claims) professional attitude is evident in the way they have nurtured relationships with manufacturers and work providers, who they consider to be business partners. That’s the mindset that is needed to succeed in today’s repair business landscape.
Again, the customer area could put a dealership to shame. How they treat their team is evident in the number of long serving members demonstrating that providing a great working environment and culture insulates you from any skills shortages because talented technicians want to work for you.
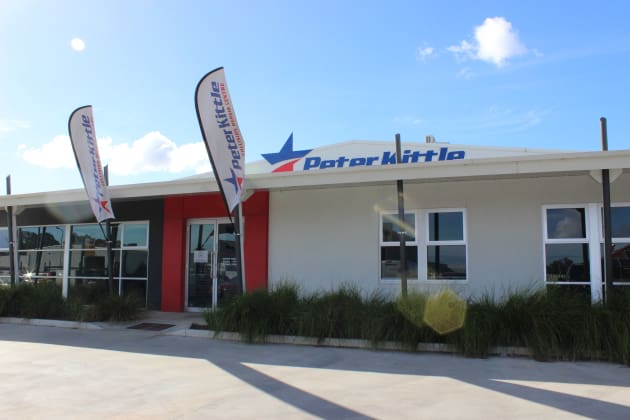
Best dealer owned shop and Operational Excellence Peter Kittle Collision
When we walked into Peter Kittle Collision in Adelaide manager Paul Whelan said ‘we do things differently here,’and the judges eyes rolled a little with a ‘yeah yeah’. Oh, we wrong, they really do things differently and extremely well, hence they also won the operational excellence award.
Paul Whelan cut his teeth in some big shops, his previous gig was at the humungous Carrisbrook Collision. He had the luxury of building this facility from scratch and the entire site is built on lean principles – he had been working for Kittles for 12 months before the first car came in for repair. They benefit from some shared dealership facilities such as the uber-cool laser car wash. Every car is washed before it enters the workshop – as you can imagine the workshop is really clean. It’s the attention to detail that impresses. Every single action has been broken down and the best product and process selected for maximum efficiency and profitability. Every cost is monitored and reviewed monthly.
From the large solar array on the roof, to the temperature controlled paint mixing room which ensures the perfect paint viscocity to the air conditioned spray booths – yes you read right. Air conditioned spray booths, especially in hot Adelaide summers ensure there is no loss of production on scorching days as well as providing the ideal painting temperatures.
It’s not just about quality but also about cost and using the least paint for the most coverage. The facility repairs around 50 cars per week – and not just Toyotas, it has to stand on its own two business feet. If we were going to split hairs... nope, no hairs to split - we couldn’t find fault. Dealerships don’t have a great track record with running bodyshops – with dealer principles often thinking that service managers can understand the complexities of dealing with insurance companies, proper quoting and the myriad variables that occur everyday in body repair. Peter Kittle haven’t made that mistake and have allowed Whelan and his team to create a sustainable repair business, although Warren Tudor who accepted the award admitted it had not been an easy journey.
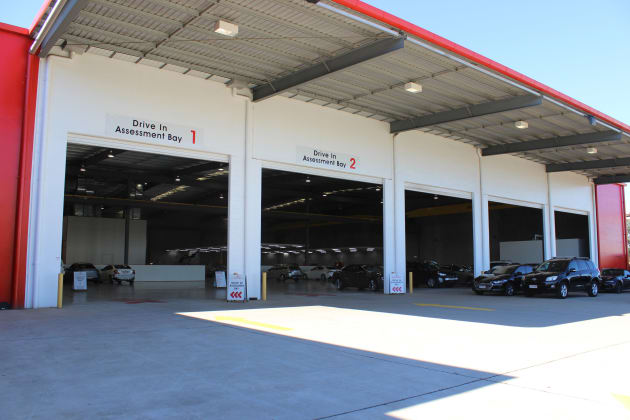
Best MSO Captial S.M.A.R.T Banyo
This is the first year that Capital S.M.A.R.T has taken part in the awards and we were very impressed. Jimmy Vais and his team have quite simply changed the face of the industry – a fact that was acknowledged in the acceptance speeches of more than one of our national winners. Capital S.M.A.R.T has a great culture full of professional, driven individuals who obviously have great pride in the company they work for. The business also has its own dedicated program for apprentices. S.M.A.R.T now employs over 1000 staff and repairs over 3,500 vehicles per week.
Capital S.M.A.R.T Banyo, Queensland can only be described as palatial. It’s an enormous building with breath-taking kerb appeal – it’s a shame that it’s in an industrial estate. It’s probably the sky high ceilings that make it seem bigger than the other sites but it is comparable with Rowville and Mulgrave in Victoria at 4,060sqm. You could safely land a plane inside – the team has plenty of room to get things right and it is superbly designed for maximum workflow. Again, everything has a process and measuring metrics. What really stands out is the top quality equipment and products sourced in Australia used throughout the repair chain. The company has phenominal buying power but it could just as easily use it to make more profit buying lesser consumables for example. Banyo has the usual bright red reception capsule seen in many of the groups workshops, with coffee machines and tables in case people have to wait. Around 130 cars per week drive in and out of Banyo and we’ve seen other high volume driveable shops that really look like they put out that many cars. Banyo has a calm atmosphere with everyone knowing what they need to do and when and the workshop is a clean at midday as it was at 8am and will be when the doors close. The bays are big and the Lowbake drive-through booths and arches are smart and productive. The layout is echoed in many other of its facilities but Banyo really took our breath away.
Best Country Repair Ken Morely Smash Repairs
This Wagga Wagga shop is run by a second generation brother and sister team Pat and Jacinta Morely. Their dad Ken, opened the doors in 1978 and retired in 2014. Since taking over the reins they’ve purpose built a stunning workshop which you have to check out on our Youtube channel. Finding and keeping staff in regional areas is a challenge. Pat says: “We wanted to be very staff focussed and make it a nice place for them to come and work. Without them we’re nothing. So we decided to add an upstairs area for staff with a small gym, bar, pool table and their lunch room.”
We had some great entries for country repairer and the standard is clearly climbing. Ken Morely Smash didn’t just win because of their incredible staff facilities. The whole presentation of the business is contemporary, sharp and state of the art. They even have a shell in reception showing the different types of construction material used in cars. Pat demonstrated strong links with the community, a rigorous customer satisfaction and quality checking process and optimum workflow. Ken Morely is proud of its facility and justifiably so, it’s a corker.
Rising Star Scott Stephens SmashTec
Stephens’ story is well told in his video entry. To have two large inner city shops by the age of 34 is impressive enough but it’s the business strategy and logistal expertise that contributed to the win. Stephens has a thoroughly 21st Century attitude towards autobody repair. He has a partnership approach to both work providers and suppliers. Monza Smash Repairs carries out the heavy hits and out of scope work that SmashTec isn’t geared to repair. Both businesses are in the same Marrickville Street and between them can repair 130 cars per week. Despite the high volume Stephens has created an excellent staff culture and the whole atmposhere is one of calm productivity. SmashTec has two compressors to ensure there’s no down time if one fails - if that’s not an impressive ‘belt and braces’ attitude we don’t know what is.
Innovation award 1Q1
The fact that a number of this year’s winners use 1Q1 and quite frankly rave about it says a lot about this workshop productivity program. Developed by father and son repairers Paul and Lauchlan Smith from Midland Smash Repairs in Perth, this system has made a hugely positive impact on production and profitability to early customers. Anything that gives repairers an edge is a boon but the simplicity and visibility of 1Q1 also helps to empower staff and create a true team atmosphere as every stage of every job can be accessed at a glance.
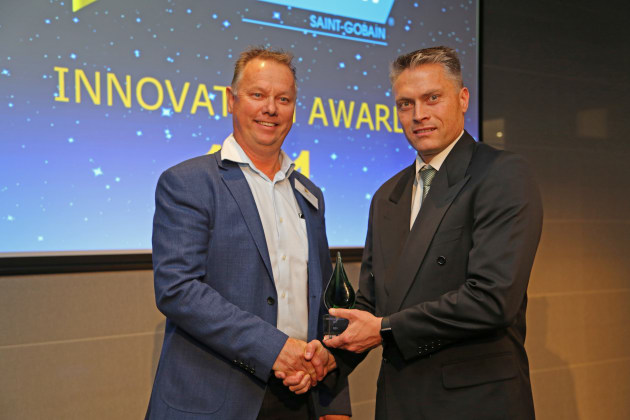